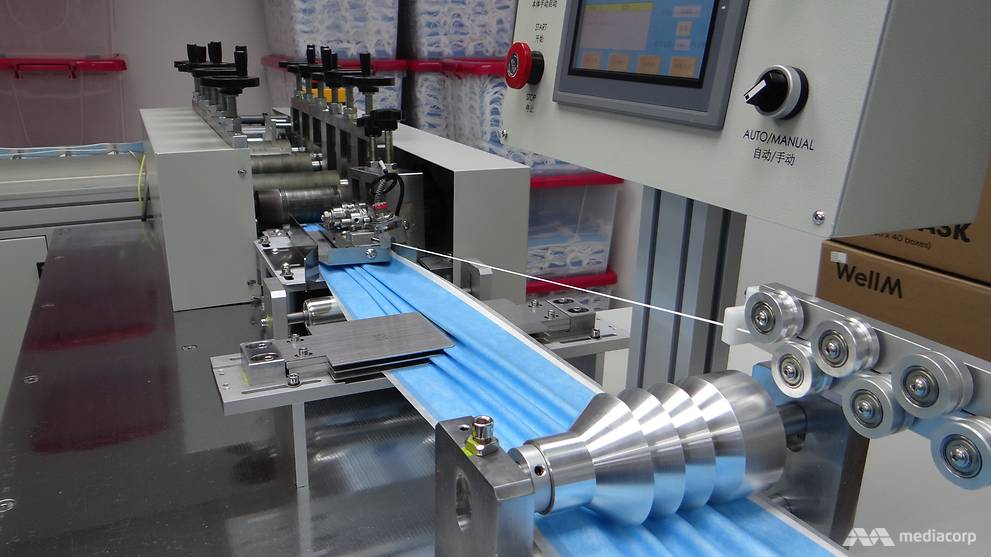
How a Singapore firm in the printing business switched to making masks amid COVID-19
by Tang See KitSINGAPORE: Arranging and checking layouts for art works, corporate banners and signages before sending them for printing have been Ms Cheang Meng Ching’s key responsibilities as a desktop publisher for the past 10 years.
But since May, her keen eye for detail has been put to quite different tasks at work.
Instead of going over page layouts on her design software, Ms Cheang now keeps tabs on three production lines that can each churn out 4,000 surgical masks an hour, as part of her role in quality-control documentation.
“It’s (a) challenge because I didn’t know anything about ISO (standards) before this,” she said.
The big change came as her employer, AVS Technologies, decided to start producing masks out of its office in Ubi – something which had little to do with the company’s primary business of distributing printing equipment and providing printing services such as 3D printing.
Other employees at the local firm have also had to step into vastly different job roles in recent months, from running the machines, checking the masks produced to packing them.
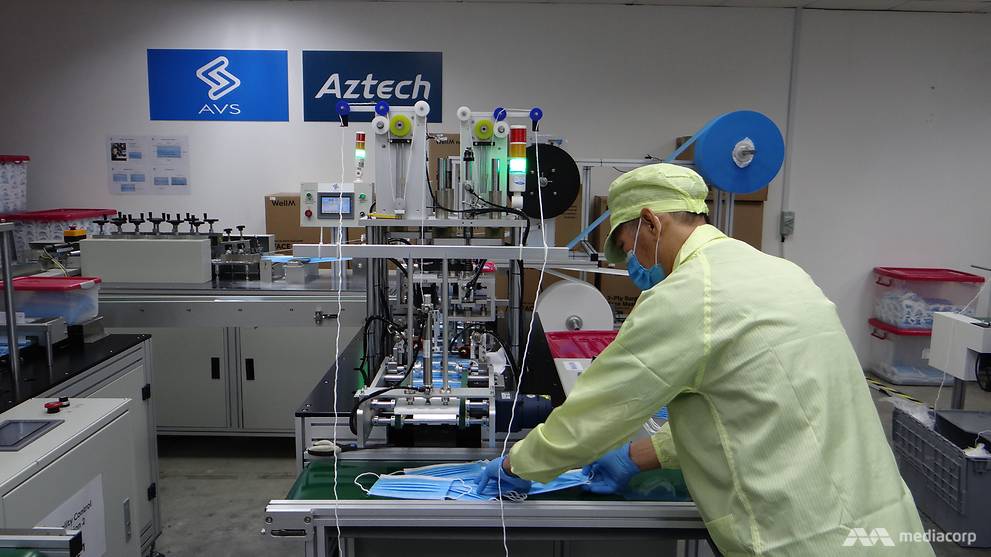
“We trained everyone – all 30 of them in accounting, graphic design, marketing, sales and administration – to go into mask production,” said AVS Technologies’ general manager Kelvin Mun.
“When we started, it was quite tough and there were days when we had to activate almost everyone,” he recalled. “But now, we are able to keep the team lean so at any one time, it’s a variation of four to 10 people from the different teams.”
Mr Mun himself has been handling customer service. “This is brand new to us so the best way to learn, I think, is to get feedback from our customers.”
WHY MAKE MASKS
It was in February when the company began toying with the idea of setting up a mask production line.
“All of us were having problems getting masks. There was a real need here,” said Mr Mun, recalling how retail stores were out of surgical masks and various countries had begun implementing export controls on medical supplies as the coronavirus outbreak developed.
Another push factor came in the form of being able to tap the expertise of Aztech Group, a separate company with whom it shares the same owner. Aztech is owned by Mr Mun’s father, Michael Mun.
“Through (their) office in China, it was possible for them to help us procure all the equipment for mask manufacturing,” said the younger Mun. “That was when we thought, ‘Why don't we do something to support local needs?’”
The decision was made in mid-April, and the company received its first machine and raw materials two weeks later.
While taking the first step seemed relatively smooth-sailing, the company paid quite a steep price.
In particular, prices for the melt-blown polypropylene – the non-woven polymer fabric that forms the filter in face masks – had multiplied on the back of global demand. Mr Mun said the company had likely bought the crucial material at prices up to 10 times higher than when the pandemic began.
“It’s like a stock market and the prices just kept going up in March, April and hit the peak in May. We had to go in to purchase the materials quickly, which means we purchased them at the peak (prices),” he recalled.
Together with two machines – one to make smaller face masks for children – which it purchased later, AVS Technologies invested about S$1 million to kickstart its mask production.
CHALLENGES
The machines, placed in a refurbished room which used to be a showroom for printers, make a humming sound as large reels of materials run through them.
The materials are first layered together before they are cut, inserted with metal nose wires into the front, the corners stamped and ear loops welded all along the fully-automated line. Workers stand at the end of the line to run quick product checks before placing the masks into plastic boxes.
These days, operations are fairly smooth and at full speed, one machine can produce about 30,000 masks in a day’s shift, said Mr Mun.
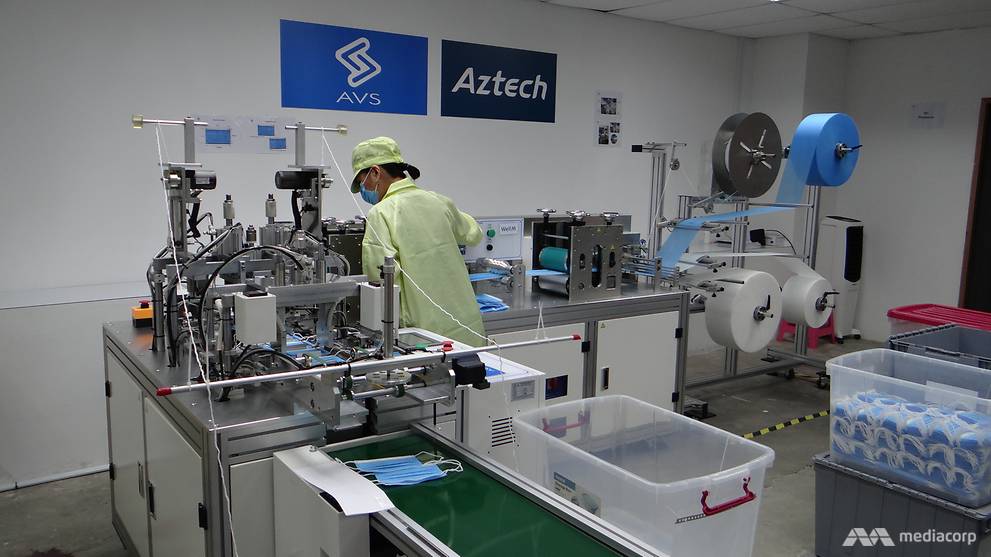
But as with all new ventures, mistakes were inevitable at the start.
Mr Mun recalled some batches that were not welded properly, resulting in ear loops falling off easily.
“There were many mechanical parts in play (and) new technologies like ultrasonic welding, that we never used before. (The masks) seemed ok when we tested them but that was because we were pulling about 10 at a time, instead of one at a time. We realised it too late and (they) were already delivered to the customers,” he told CNA.
The company later did an exchange for these masks – about 4,000 pieces, which it later discarded. After which, the team refined its checking process.
Mr Mun noted that checking and packing were the “bottlenecks” of the production process, especially when orders built up towards the end of May before the "circuit breaker" was lifted.
“Apart from those conducting the checks before packing, the person running the machine must also be very sharp to identify the problems,” he said. “The pressure can be quite high.”
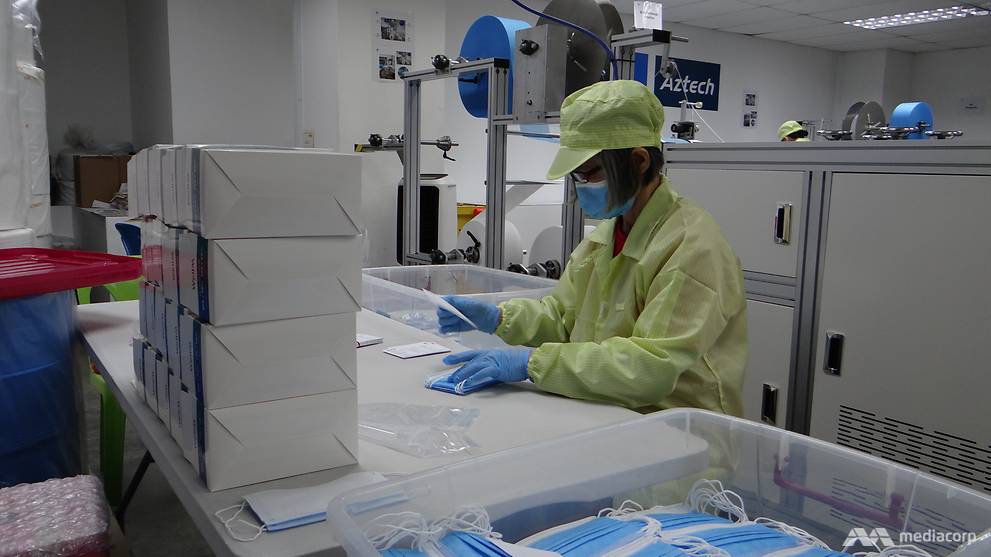
To assure customers about the reliability of its masks, AVS Technologies has obtained a licence from the Health Sciences Authority. Its brand of surgical masks, called WellM, also has the European Union approval, otherwise known as a CE mark.
Test reports of its masks are also available on its website.
“We spent time and effort on all these tests to make sure that people buying know that our masks are safe,” said Mr Mun. “We are not making cheap products and trying to make money out of this pandemic.”
DIVERSIFICATION?
Since starting production in May, the company said it has sold about 2 million masks. It has also added face shields and hand sanitisers to its repertoire more recently.
All of its products are currently sold via its website, with deliveries being made by taxi drivers who wish to earn extra income.
As part of its next step, the company has begun selling its masks to Canada and Malaysia, with other markets such as United States and Europe next on its list.
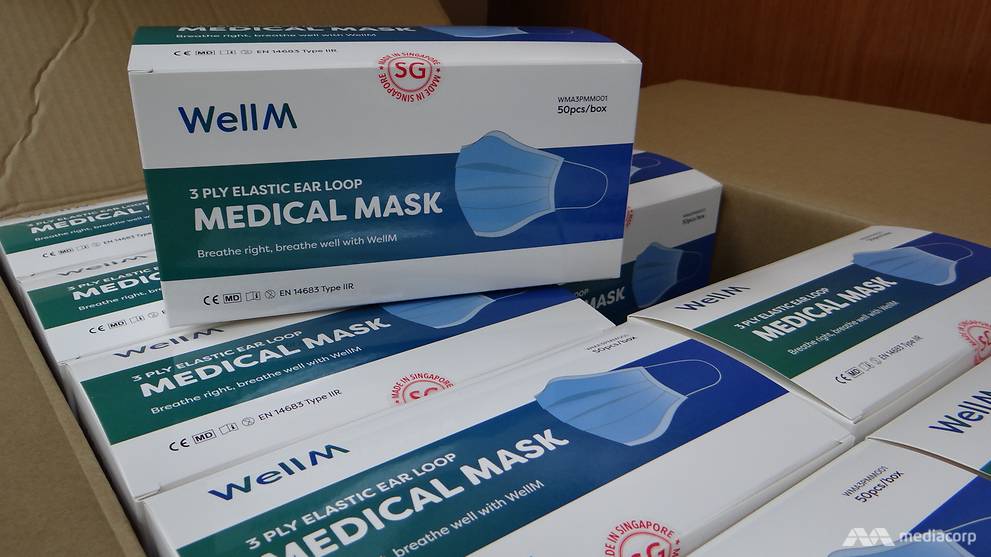
Asked if making masks could be a key part of its business moving forward, Mr Mun said prices of surgical masks have retreated globally. Given that the company is still using raw materials that it bought when prices were at the peak, it has been hard for the new local brand to compete with much bigger foreign brands in terms of price.
“Prices of face masks have been coming down so I don’t think this can be sustainable in the long term given the cost to produce in Singapore … but we will not give it up though.
“We will look at maintaining at least one line in future; maybe not running every day but any time we need to press the panic button, we are ready to start producing.”
Mr Mun noted that the company's printing business has been affected by the cancellations of major events and trade shows. On whether the company should have saved for rainy days instead of making the hefty investment into mask-making, he said: “I know if we were to go through the usual business processes of whether to do or not, it wouldn’t have made sense because it’s quite high risk.
“But we are generally still ok so we’ll like to think that this is an opportunity to build up additional capabilities and also do our part to build up local production of masks at a time like this.”
READ: Companies seek new opportunities to stay afloat amid COVID-19 pandemic
Through the process, the company has picked up knowledge about the production of medical equipment, which it is hoping could complement its more advanced capabilities in printing.
“Now that we know the requirements of making medical equipment, we are trying to link what we have learnt back to our expertise in printing, which consists of 3D printing and milling engineering … and see if we can explore any opportunities in medical manufacturing,” said Mr Mun.
“The Government has made it very clear that … businesses need to really think about diversifying."
More importantly, it said it has received positive feedback about its masks.
“Some customers wrote back to tell us that their kids loved the masks and they were easy to breathe in,” said Mr Mun. “Reviews like these make us happy and accomplished.”
BOOKMARK THIS: Our comprehensive coverage of the coronavirus outbreak and its developments
Download our app or subscribe to our Telegram channel for the latest updates on the coronavirus outbreak: https://cna.asia/telegram