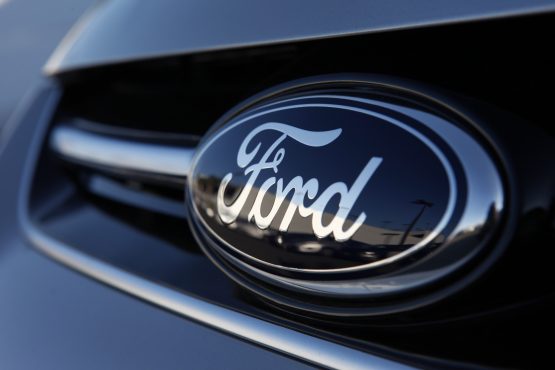
Ford invests around R138m in a new Silverton plant facility
Motor giant aims to double production to 200 000 units a year over the next three to four years.
by Roy CokayneThe Ford Motor Company of Southern Africa (FMCSA) has invested about €7 million (R138.74 million)* in relocating and upgrading its wheel and tyre facility as part of its ongoing drive to improve production efficiencies and capacity at its Silverton Assembly Plant in Pretoria.
The plant produces the Ranger (bakkie) and Everest sport utility vehicle for the domestic market and for export to more than 100 markets around the world.
The investment in the new 5 000m2 wheel and tyre facility has been made against the backdrop of FMCSA MD Neale Hill confirming at the launch of the Tshwane Automotive Special Economic Zone (TASEZ) in November 2019 that its vision is to double production at the Silverton plant, as part of a journey to become the largest Ranger manufacturing facility in the world.
Read:
Automotive component suppliers commit R4.3bn to establish operations in Tshwane
R3.5bn to be invested in first phase of Tshwane’s Automotive SEZ
Hill said the plant has an annual production capacity of 168 000 units but was then producing just over 100 000 units a year and its plan was to double production to 200 000 units a year over the next three to four years.
Boosting efficiency
Post the Covid-19 hard lockdown, the Silverton plant is assembling about 480 vehicles a day based on two eight-hour shifts, which translates to about 2 400 tyres fitted on rims and supplied to the plant’s trim, chassis and final (TCF) line where the vehicles are assembled.
FMCSA corporate communications manager Duduzile Nxele said the old facility had the capacity to produce up to 1 760 rims and tyres daily, making the improvements and upgrades quite significant.
FMCSA vice president of operations Ockert Berry said last week that construction of the new, larger, wheel and tyre facility commenced in September 2019 to replace the existing 2 993m2 facility.
Berry said it was completed within just over three months and began operations in January before South Africa went into Covid-19 lockdown in March this year.
But with the Silverton plant back up and running since the beginning of June and one new vehicle again coming off the line every two minutes, Berry said the benefits of the new facility are already evident.
“We are always working on ways to enhance our production processes to make the plant more efficient, reduce our cycle times, improve capacity, and offer the best working conditions for our employees.
“The decision to build a new wheel and tyre facility was based on all of these objectives, with the clean-sheet design allowing us to incorporate the latest technologies and equipment to optimise our current operations and easily introduce future upgrades and expansion when required,” he said.
FMCSA TCF vehicle operations manufacturing engineering manager Yuliia Varchuk said the new facility has allowed them to increase production efficiency and handle greater complexity for the wide range of rims and tyres fitted to the Ranger and Everest models.
Pushing productivity
Varchuk said that with a fitted wheel and tyre coming out of this facility about every 15 seconds, the fitment and balancing needs to be seamlessly integrated into the overall workflow and the new facility has significantly improved productivity in this area.
“This will be further enhanced when an overhead wheel and tyre delivery conveyor installation is completed by September next year. This conveyor will feed assembled wheels and tyres from the new facility directly to the vehicle assembly point of fit in sequence, replacing current manual delivery process, which will help reduce traffic in the plant,” she said.
The new facility is able to fit a wide range of sizes while the specialised rims and reinforced, high-performance off-road tyres used on the Ranger Raptor pose an additional challenge because each fitted unit weighs 40kg but the facility is geared to easily handle this.
“From the outset, we designed the new facility to make it relatively easy and cost-effective to further increase capacity based on future expansion possibilities, and to handle an even wider range of wheel sizes,” Varchuk said.
In line with the Silverton assembly plant’s advanced technologies, the wheel and tyre facility is almost entirely automated – with the supply of the appropriate rims and tyres electronically synchronised according to the plant’s daily build schedule – and takes into account the final destination market and each vehicle’s unique specification.
Nxele said the old facility was also automated but the upgrade has improved the technology and specifically increased the capacity of the facility.
She said the old facility was manned by about 26 individuals over two shifts and this has increased to 32 individuals over two shifts in the new facility because of the increase in volume and the improvement and addition of technology standards.
Read: SA’s automotive industry achieves record trade surplus
* €1 = R19.82